EHAB Weather Ledger – Guide to the Effective Deployment of IoT on construction sites
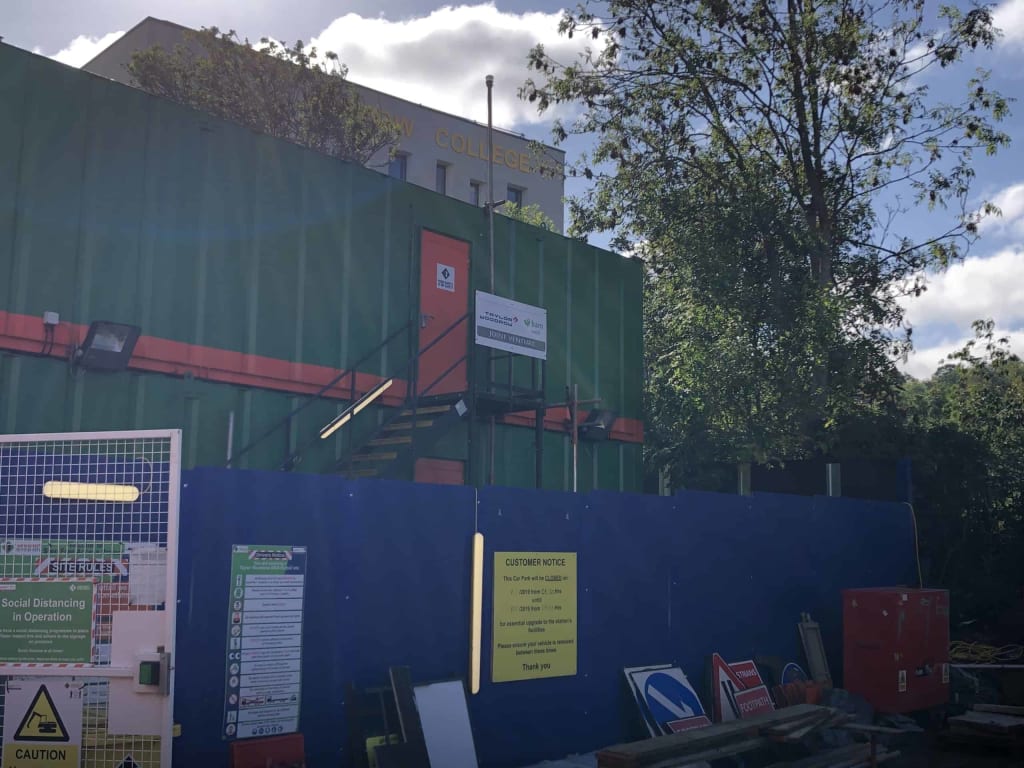
The use of data in the construction industry and deployment of IoT on construction sites to drive better decision making, has huge benefits, helping project managers to make decisions quicker based on the real situation on the ground such as weather conditions and movement of materials.
One key technology for helping capture situational data, is through the use of IoT (Internet of Things) sensors. But many construction sites have challenging site conditions that can often be remote or without power and connectivity set up from day one along with disruptive activities. Therefore how can you best go about deploying IoT IoT on construction sites?
We at CPC have been supporting one such trial through an Innovate UK transforming construction project the ‘Weather Ledger’ helping the startup EHAB bring a pioneering weather risk management platform to market, including deployment of the solution across 5 construction sites. As part of this, Connected Places Catapult and our partners, have been capturing the learnings to create a guide to IoT, to help others know where to start with IoT from planning your site, through to dismantling devices at the end of their life (where not forming part of the ongoing infrastructure).
Introducing the Guide to the effective deployment of IoT on construction sites
The guide has been produced based on the learnings derived from the real world experiences and activities that have taken place as part of an Innovate UK Transforming Construction challenge funded project, ‘The Weather Ledger’. The project used IoT (Internet of Things) and DLT (Distributed Ledger Technology) to automate the collection of weather related clauses in standard NEC construction contracts.
It has been authored by the Connected Places Catapult, in collaboration with project partners led by EHABITATION (EHAB) Ltd, Digital Catapult providing IoT and DLT deployment expertise, Ferrovial and BAM Nuttall providing pilot sites, and Clyde and Co. with legal expertise who are joint project partners for The Weather Ledger project.
What does the guide cover?
The guide covers the fundamental aspects for achieving best practive when it comes to Planning, Procurement, Deployment, Operation and Recovery of IoT devices and their associated infrastructure in a construction site context.
For example, at the the Deployment stage, considering site issues including power and connectivity, where to site and position devices, specific considerations for weather sensors, how to mitigate impacts from the local environment, security and protection controls such as protection against tampering and vandalism, calibration and guidance on remote monitoring of devices.
Principles for Effective Deployment
The guide defines successful IoT deployment is seen as being: straightforward to install, trouble-free, reliable, secure, trustworthy, and resilient.
Overall, it is based on five key principles that should be considered to better guide a successful IoT deployment:
1. Good Data Management
Ensure appropriate controls are in place to provide reliability and data integrity that is appropriate to its intended use.
Data access, and recovery and therefore the controls that need to be in place are highly dependent upon the purpose of the deployment and how critical the data is that is being collected.
The accuracy and reliability of IoT data plays an important role in being able to effectively respond to events in a timely manner. Several sources need to be accessed and compared to ensure that received data from the IoT devices are trustworthy and reliable.
Backup processes and procedures should be in place to ensure that if and when there is data loss at some point within the chain it can be recovered, validated and ingested without the risk of spurious or duplicate records.
2. Robust Testing and Performance
Ensure that the performance of the selected IoT devices satisfy the specific requirements of the deployment.
Select IoT devices that have been tested by an appropriate and accredited third party test laboratory (accredited to ISO 17025) to support the verification of performance against manufacturers claims.
3. Self sufficiency and simplicity
Ensure that the IoT device can be installed and operated with minimum effort for non-technical people (ideally ‘out of the box’ by users without requiring a site visit from a third party).
In most instances, once a sensor is deployed, it is difficult, time consuming and disruptive to upgrade or replace a device.
A device that is self-contained (e.g. serviceable, stores data, self-powering) and simple to use as possible (plug and play) is recommended.
4. Proactive/Dynamic Maintenance
Ensure that the IoT device reports health data regularly, securely capable of reporting important factors like battery level, signal reception, data storage, data transfer loss etc. Ideally IoT devices should be capable of sending alerts if its health data drops below the predefined thresholds. This feature can be helpful to mitigate any problems before any potential failure such as loss of data.
Human monitoring onsite in remote locations is costly and arduous. In the absence of an established interface, if a device goes offline, there is no chance of connecting to it. In this case, it either has to be retrieved for repair, recalibrated or replaced depending on the nature of the problem.
Get in touch
This guide has been developed by learning from real world application but we are keen for this learning not to stop here.
We hope others will find this guide useful and we are keen to hear from others looking to deploy IoT in construction. If you would like to provide any feedback on this guide or share learnings from your IoT project we are happy to hear.
Please get in touch with the City Standards Team via info@cp.catapult.org.uk