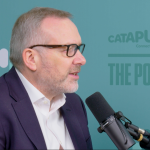
Transforming housing construction
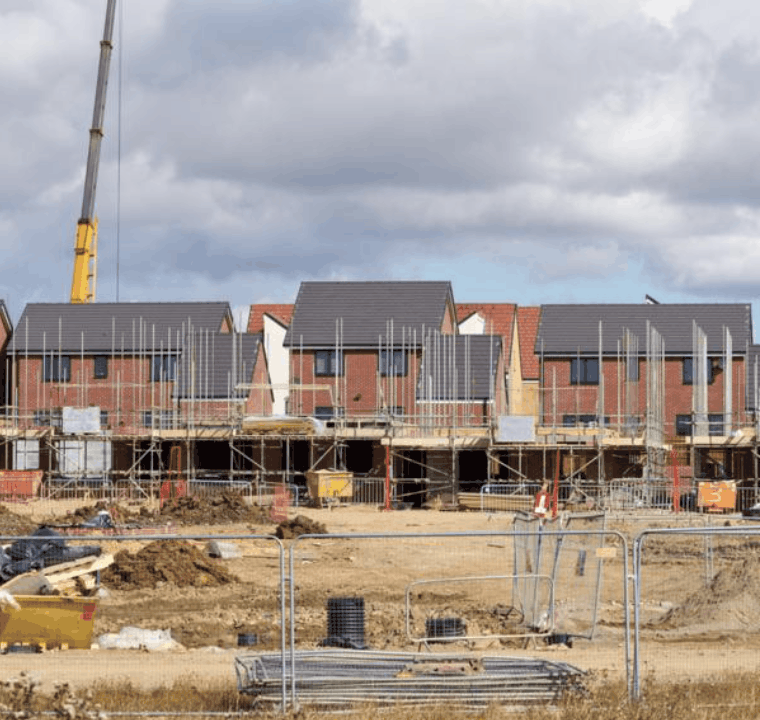
The UK Government has an aim to increase home building from the current levels of just over 200,000 to 300,000 per year. In this week’s guest blog in our Future of Housing series, Mike Pitts, Deputy Challenge Director at Innovate UK, says new digital manufacturing technologies can help meet the productivity challenge and deliver higher quality, energy-efficient buildings at the same time.
Construction is labour intensive. It relies on the availability of skilled workers, and these are in decline due to the age profile of the workforce and the reliance on migrant labour, mainly from the EU. To boost production, the sector needs to adopt more productive and innovative methods of constructing houses which will go along way to transforming the housing construction sector.
Those methods may also help with quality issues. Can you imagine making cars by delivering the raw materials to your driveway and then getting a succession of skilled labourers to come and carry out their specific role in turning them into parts before assembling a whole car? This is the way we make homes. The inefficiency of doing everything onsite is clear. For every house that is completed, on average seven tonnes of waste is produced, much of which is brought to the site and then discarded without ever being used. This also affects quality. Buildings that don’t perform as expected, they often aren't inclusive and/or need extension work after supposed completion, are common.
The Transforming Construction programme, under the government’s Industrial Strategy, is setting out to tackle issues like this and accelerate the adoption of the kind of digital manufacturing practices that have transformed other sectors including aerospace and automotive. The programme is managed by UK Research and Innovation (UKRI) and is the biggest public investment in construction innovation for a generation.
Beyond energy efficiency
The programme is already funding activities with both small and large house builders, helping them to work with digital design, project and building monitoring, and the factory production of building parts. This expedites onsite work, boosts build quality, and creates new jobs in the process. Better made homes will require less energy to run, but we want to go further than that. We want to make it easier and cheaper to incorporate energy generation technologies into a building, effectively turning your home into a power station; raising the prospect of no energy bills, payment for excess energy, or free refuelling of your electric car.
That’s all fine for new buildings you might say, but what about the existing housing stock that is energy inefficient and uncomfortable to live in? The term used for upgrading the insulation and energy technology of old buildings is ‘retrofit’. A lot of work has been done to show retrofit is technically possible for UK homes and is happening at scale in other countries. For retrofit to be achievable at a cost that is mitigated by energy savings, it must happen at scale, in an organised manufacturing-led way. As a future innovation programme, we envisage a large-scale scheme that would bring together the retrofit supply chain and involve landlords proactively seeking to upgrade their stock. This could achieve the critical mass required to bring down the cost and increase the scale at which retrofit happens. To that end, we are keen to hear from industry and landlords who want to combine their plans with this potential major programme.
In order to do this, and encourage innovation in the construction sector, we’ve set up the Transforming Construction challenge. We want to see the industry producing safe, healthy, efficient houses using the latest digital manufacturing techniques. This approach will help us meet the UK’s national infrastructure programme target of £650 billion worth of projects by 2025 head-on. Through the challenge, we will be supporting the sector as it adopts new technologies that will ultimately mean buildings are constructed 50% faster, 33% cheaper and with half the lifetime carbon emissions. In order to bring about this change, UKRI is turning to innovative players in industry and research to disrupt construction, increase productivity and open global markets for efficient buildings.
You can follow Mike Pitts on Twitter @pittso.
This guest blog is one in a series and is part of our new Future of Housing programme. Find out more about our work in this area by visiting our new Future of Housing knowledge hub.
Are you interested in sharing your insights in this area? If you’d like to let us know about some of the projects you’re working on in this space, please email futureofhousing@cp.catapult.org.uk.
Our Future of Housing blog series is intended as a platform for open debate. Views expressed are not necessarily those of the Connected Places Catapult.