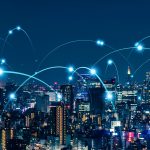
Durable plastic components pulled together for transport applications
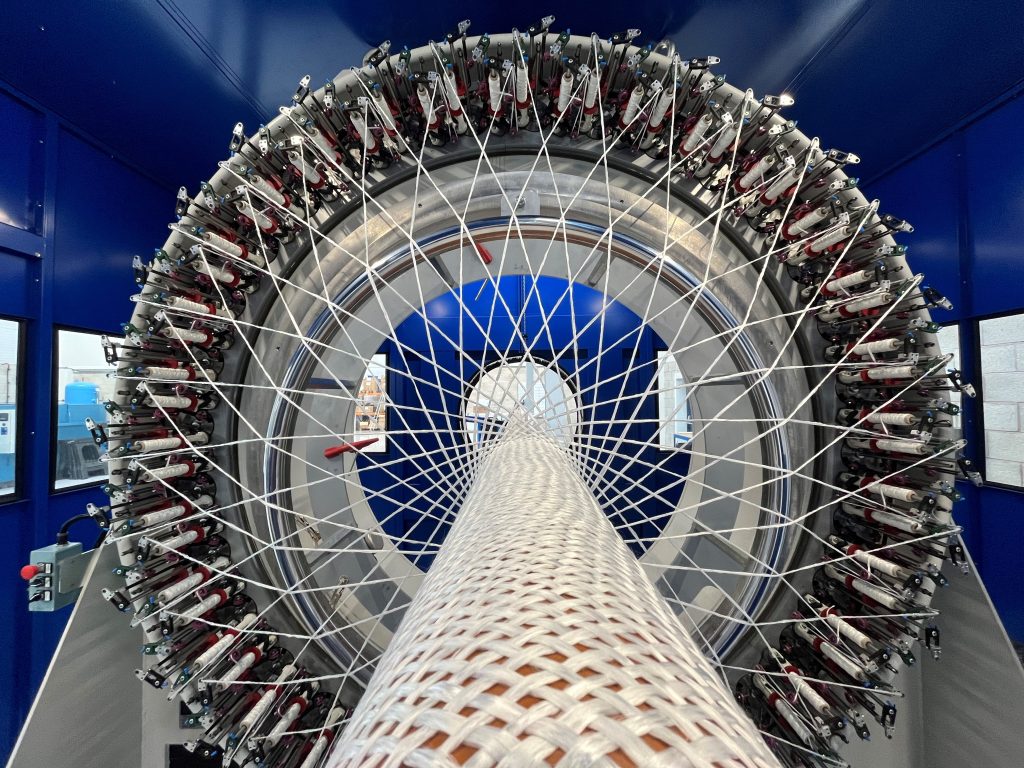
East Midlands manufacturer Composite Braiding is participating in a second round of the Clean Futures Accelerator with Connected Places Catapult, after successfully developing a small but essential component for automotive use.
The company created a new form of rivet to secure sections of thermoplastic compositive material together for the chassis of an electric vehicle, as part of the first cohort of the programme in 2023, with support from Coventry University.
Now the firm has switched its attention to rail, and is taking part in cohort two of Clean Futures to develop structural components for new overhead line equipment, with support from research and technology organisation BCIMO.
“We won a sustainability award for circularity in construction for our rivet a few months ago from trade association Composites UK,” explains Composite Braiding director Steve Barbour who has launched a patent for the component.
“The rivet joins together three sections of carbon and nylon composite for use in the cab structure of a 3.5t electric van, without the need for adhesives or metallic parts.”
Joining composites together is a very important but difficult specialism, adds Steve. “The programme allowed us to have a good think about how we can achieve this at volume, and in a way which is economically viable.”
Now the Watt Electric Vehicle Company – which specified structural components for the composite cab, along with the special rivets – is looking to take its prototype van into production.
“The Clean Futures Accelerator delivered far more than I had initially expected,” Steve says of participating in cohort one. “It provided a whole set of other topics and business-related issues to work through. It was very much a programme that added value.
“It also helped to broaden the company’s perspectives,” he adds. “I was able to put some staff into areas where they weren't previously exposed, to develop their skills and broaden the team’s capability.”
Moving from automotive to rail
Steve thought his time with Clean Futures had come to an end when the first season of programme finished, but decided to apply for year two when he realised the accelerator also focuses on rail infrastructure.
Keen to make a move into railways, he secured several letters of support from tier one rail suppliers for Composite Braiding to take part in Clean Futures again, this time to design composite alternatives to steel and concrete equipment.

Participation in the project will involve designing and trialling new infrastructure from composite material, and calculating the carbon savings expected.
Steve has been working with composites for over 20 years and says they offer a lightweight, easier to assemble alternative to conventional construction materials. Composites can also reduce maintenance need which, in the case of rail work, means improved safety as there are fewer “boots on ballast”.
Reduction in the volume of concrete and steel consumed also means lower carbon emissions during manufacture, he says.
“Composites are very much an enabler towards net zero. If you take a vehicle, the lighter it is, the fewer emissions it has. In a few years’ time, composites will be much more accepted because people will understand what benefits they bring.
“There is no shortage of innovation in the UK and no shortage of startups. But what there is a great shortage of is the ability to scale businesses, so Clean Futures is a great tool to help you get there.”
Braiding explained
Composite Braiding manufactures structural tubes, poles and beams of various shapes and sizes. Conventionally they can take a long time to process, so Steve developed a way of producing higher quantities of product at lower cost; introducing an element of automation into the process.
He invested in and modified a braiding machine, which essentially “takes individual strands of material, and weaves a sock” to blend together two materials such as glass fibre with a thermoplastic such as nylon into a tube that is both lightweight and flexible. The machine can weave around 50mm a second, or around one mile a day.
Strength is achieved by adding heat and pressure to create a stiff material “as strong as steel, but 70% lighter”. The process of creating a tube, Steve adds, can take as little as five minutes.
“It was great to work alongside other companies on cohort one of Clean Futures who are doing brilliant things, exchange views and collaborate. I am looking forward to more with the second cohort.”
Latest impact statistics from the Clean Futures Accelerator show the programme has generated £2.6 million for SMEs through contracts or research and development funding, with a further £43 million in the committed pipeline. Click here for further details about the programme’s impact.
Clean Futures is being led by Connected Places Catapult in collaboration with BCIMO, Coventry University and CU Services Limited. It is part of the wider West Midlands Innovation Accelerator, funded by UK Government and delivered by Innovate UK, which is designed to bolster the region’s innovation and R&D capability and spark commercial growth and investment.
